Participating in change for a better future is in our DNA. And one such way that we did it in the real world is through a series of prestigious projects around Heave Compensating Gangways or Motion Compensating Gangways.
A NEW THOUGHT FOR TOMORROW
The last few years have witnessed a paradigm shift in switching over to renewable energy. The offshore industry has taken the challenge head on and has adapted to it. On this front, one of the major goals set by European countries has been to install a record number of Windmills across the Northern Sea. By all means, it is an optimistic goal to achieve by 2030. But they are not alone. Various sectors of the offshore industry have come forward to support this positive approach. However, these wind mills also needto be maintained over time to keep up with a range of diverse requirements.
NEED FOR UNIQUE GANGWAYS
Reduced impact of vessel motions: To cater to the requirements of these windmills, offshore vessels need to be mobilized with walk-to-work systems on the deck, within a short period of time. These systems are basically specialized Heave Compensating Gangways that assist in transferring Personnel at various levels, without feeling any impact of vessel motions.
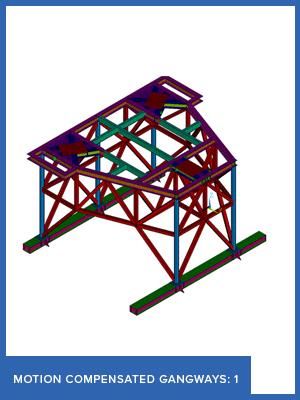
Safer and more seamless: Apart from serving as a walk-to-work system, the gangways are also used at various offshore platforms for transfer of personnel and cargo. The motion compensation of these gangways adds an edge to safety as against traditional approach.
Game changer in its own way: In several ways, Heave Compensating Gangways can emerge as a game-changing technology to implement in the Indian waters. It can be used to back-up India’s vision to install a great number of wind mills, thereby helping it achieve the goals of the PARIS AGREEMENT.
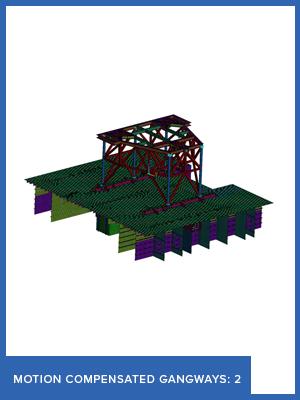
WHERE VEDAM FITS IN
We are proud to be part of this green revolution, and have assisted clients with a complete design package (from basic design to class approval) for installation of Heave Compensating systems on offshore vessels. What’s more, we have also provided a dedicated deck arrangement and securing of supporting Auxiliaries and equipment. We also accelerated our speed and have managed to execute the project at an average turnover time of 2 weeks flat.
We call it being a part of change, and doing it in time.